Introduction
The aim of this toolbox talk is to increase awareness on the the safe use of power tools.
The use of regular toolbox talks, if done effectively, will significantly improve the safety culture within your organisation. This will increase the safety awareness of the workers, and as a result reduce the likelihood of accidents and unsafe occurrences.
Legislation references
- Health & Safety at Work Act 1974
- Management of Health & Safety at Work Regulations 1999
- PUWER (Provision and Use of Work Equipment Regulations)
Why do we have training?
- Reduce accidents
- It’s a legal requirement
- Improves work performance
Safe use and provision of power tools
Employers are required to maintain equipment at regular intervals.
Employees are required to inspect the equipment every time they us it.
The person using a piece of equipment must be adequately trained. This includes the manager / supervisor in charge of the user.
Training must include the following:
- use of the equipment
- hazards arising from use
- precautions to be taken
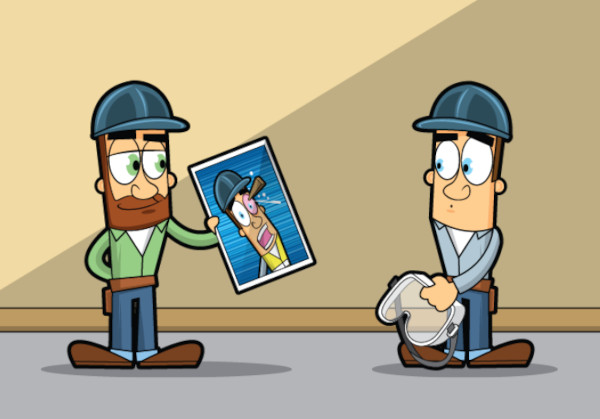
Examples of pre-use inspections
Checking electrical plugs:
- verifying the correct voltage
- undamaged
- pins are not bent
- cable is securely clamped on the outer sheath and not the wires
- RCD’s for 240V
- damage such as cuts
- splits
- bad scuffs / abrasions / taped joints
- nothing more than minor scuffing
- unwind extension leads
- undamaged
- cracks
- loose / missing screws
- melted plastic
- cable secured by outer sheath, not the wires
- label fitted and clearly showing information
- controls working, not sticking
- PAT (portable appliance test) certificate / sticker in date
- correct for the machine
- undamaged
- fixed securely
- correct for the task
Pre-inspecting accessories:
- correct for the machine
- correctly fitted
- undamaged
- suitable for the job / task