Machinery Safety
Expert guidance, advice and support from our in-house professional and experienced consultant engineering team.
Our detailed approach to design risk assessment consistently achieves risk elimination through systematic and inherent design improvements.
Fully compliant safety requirement specifications and continued support, all the way through to commissioning, to achieve UKCA mark certification.
Complete life cycle support for all aspects of machinery safety engineering to drive significant performance improvements and safety compliance.
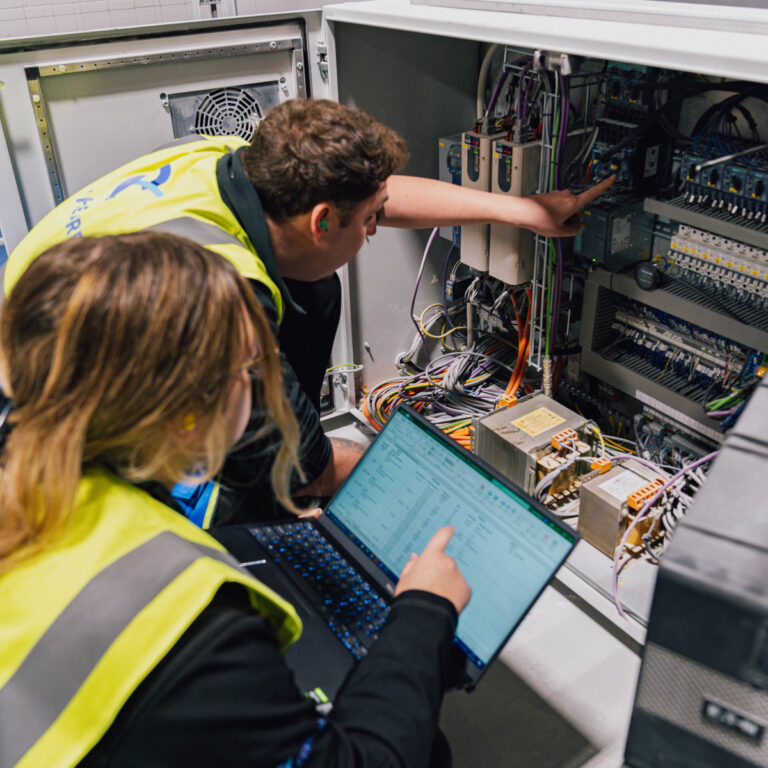
Our approach
From early involvement during the design stages to final validation of safety performance in the commissioning stages. Our in-house team of machinery safety engineers take a pragmatic and strategic approach to verifying compliance with relevant standards and UK conformity assessment requirements.
Through action based strategies to ensure compliance with the Supply of Machinery Regulations, Cenheard provides a wide range of OEM’s, machinery designers and system integrators with third party reassurance of regulatory compliance.
Contact our engineering team today to get the specific expertise you need for your next project.
Design risk assessments
Full life cycle design risk assessment inline with BS EN ISO 12100 – the general principles for design – risk assessment and risk reduction. Cenheard engineering team, have a thorough understanding of the standardised methods and requirements for risk assessment and reduction at the design stage of machinery.
Our detailed approach identifies realistic opportunities for performance improvements, while our diverse manufacturing knowledge finds solutions that enhance overall output and design viability.
Getting third party input at the early stages of design, mitigates complications further down the design process. Cenheard’s engineering team helps add noticeable value to design teams by offering an impartial view on design ideas that ultimately aids in the resulting compliance of machinery and equipment.
Safety requirement specifications (SRS)
SRS (safety requirement specifications) provide detailed assessment and finely tuned specifications for machinery safety. Determining PLr (required performance level) specifications and wiring categories from the outset of machinery designs, allows clients to achieve more robust pricing models and costing assessments.
With a wide knowledge of technological applications, Cenheard engineering team have the experience of utilising technology for safety applications in the real world. Knowing which technologies work best for particular environments can prove invaluable at the design stages and can ensure a smooth installation and commissioning process. Keeping end-users happy by minimising downtime and keeping to tight deadlines.
Guarding design specifications
Understanding and assessing against the guarding design requirements of BS EN ISO 14120, our in-house professionals can provide assurances of adequate machine guarding construction.
Getting reach distances aligned with BS EN ISO 13857 at the design stages mitigates nonconformities with PUWER for end users. All end users must comply with the dangerous parts of machinery requirements of PUWER, by getting designs right before the installation stage, you can keep end users coming back to purchase ever more compliant machinery and equipment.
Safeguard selection and positioning
Light guards, floor scanners, and two handed controls all have their part to play in mitigating operational risk without fully guarding off plant, machinery and equipment. Each have their own standards to specify safe design methodologies and requirements.
With Cenheard’s expansive experience with a diverse range of applications, our engineering team have the expertise to support with, or fully develop, safety specifications and design principles.
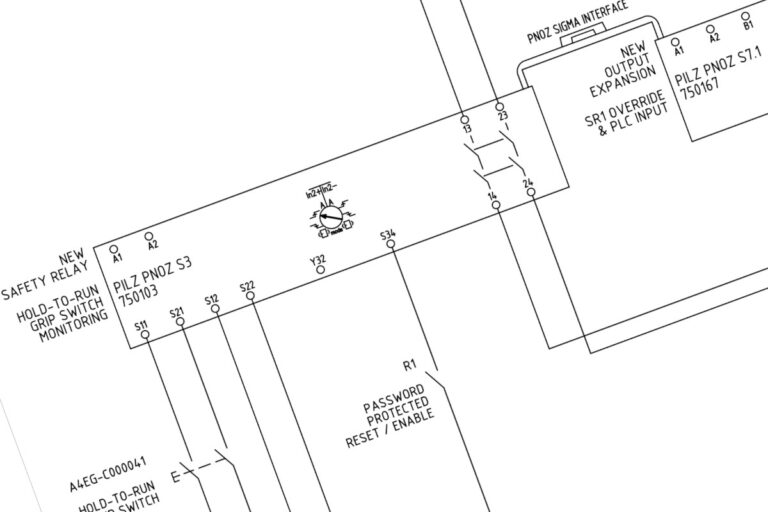
Design reviews and collaborations
With a diverse range of skills and expertise, Cenheard engineering team can offer a bespoke range of collaborative design ideas and solutions to risk assessment findings and technical specifications.
During design stages, our professional team can help review schematics and design proposals to verify compliance at the earliest opportunity.
Cenheard have helped to support a wide range of clients embed compliant designs into their machinery before building has even begun, mitigating the need for expensive design changes during manufacture.
Safety function testing
Verification, validation and on site safety circuit testing forms a vital part of any machine commissioning process. Guaranteeing ‘as designed’ operation and providing peace of mind that safety systems operate as intended.
From testing individual machines to testing entire production lines, our in-house professionals have the expertise to verify the installation of machinery safety systems.
Adjacent machine interfaces are critical on larger installations where multiple OEM’s and machine manufacturers meet. Such interfaces can create instances of unsafe stoppages and access to dangers parts of machinery. Correctly assessing the final installation is critical in ensuring operator and end-user safety. With Cenheard’s vast knowledge of cross manufacturer integrations, our in-house engineering team can provide peace of mind for end-users and system integrators.
UKCA mark certification
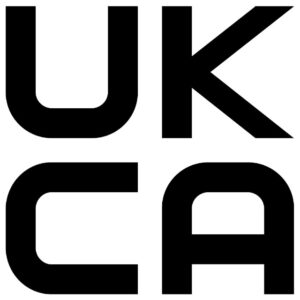
Complete UK conformity assessments, UKCA marking and complete technical file development. From machine refurbishments to full line assessments of assembled machinery.
Cenheard engineering team continue to help certify machines and complete productions lines against UK conformity assessment requirements. Helping end-users, OEM’s and system integrators achieve compliance with the Supply of Machinery Regulations.